KYB Shocks are available in standard and upgraded, Gas and oil filled! See selection on right side of screen.
All vehicles are equipped with a form of suspension damping control. They may use hydraulic fluid, air, gas or be electrically controlled. The two most widely used internal designs are twin-tube and mono-tube.
Twin-tube vs. Mono-tube
The mono-tube design has a single cylinder:
The cylinder is divided into two sections: A fluid area and a gas chamber. The piston and shaft move in the fluid portion. It uses one fluid valve assembly in the piston. The diameter of the single working cylinder and piston valve is larger than in a twin tube even though the outside dimensions of each may the same. There is no need for an air or gas in the fluid area so the valve can operate more responsively and without any aeration or performance fade. The high pressure gas chamber is separated from the fluid area by a floating piston & seal. That provides an expansion area for the excess fluid movement during the compression stroke. On more aggressive movement the floating piston is pushed further into the gas chamber which increases gas pressure quickly and provides additional damping force. Because of its higher performance capabilities, the mono-tube design is used as original equipment on some vehicles and offered as an upgrade on vehicles that came equipped with the twin tube design.
The twin-tube design has two cylinders:
The inner, or working cylinder, is where the piston and shaft move up and down. The outer cylinder serves as a reservoir for the hydraulic fluid. There are fluid valves in the piston and in the stationary base valve. The base valve controls fluid flow between both cylinders and provides some of the damping force. The valves in the piston control most of the damping. The term Gas Shock usually refers to the same twin-tube design, but with one improvement. Low pressure Nitrogen gas is added to replace any oxygen air. The effect lessens aeration and performance fade.
All vehicles are equipped with a form of suspension damping control. They may use hydraulic fluid, air, gas or be electrically controlled. The two most widely used internal designs are twin-tube and mono-tube.
Twin-tube vs. Mono-tube
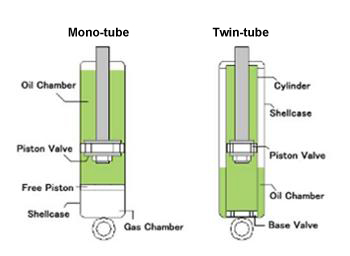
The cylinder is divided into two sections: A fluid area and a gas chamber. The piston and shaft move in the fluid portion. It uses one fluid valve assembly in the piston. The diameter of the single working cylinder and piston valve is larger than in a twin tube even though the outside dimensions of each may the same. There is no need for an air or gas in the fluid area so the valve can operate more responsively and without any aeration or performance fade. The high pressure gas chamber is separated from the fluid area by a floating piston & seal. That provides an expansion area for the excess fluid movement during the compression stroke. On more aggressive movement the floating piston is pushed further into the gas chamber which increases gas pressure quickly and provides additional damping force. Because of its higher performance capabilities, the mono-tube design is used as original equipment on some vehicles and offered as an upgrade on vehicles that came equipped with the twin tube design.
The twin-tube design has two cylinders:
The inner, or working cylinder, is where the piston and shaft move up and down. The outer cylinder serves as a reservoir for the hydraulic fluid. There are fluid valves in the piston and in the stationary base valve. The base valve controls fluid flow between both cylinders and provides some of the damping force. The valves in the piston control most of the damping. The term Gas Shock usually refers to the same twin-tube design, but with one improvement. Low pressure Nitrogen gas is added to replace any oxygen air. The effect lessens aeration and performance fade.
KYB Shocks are available in standard and upgraded, Gas and oil filled! See selection on right side of screen.
All vehicles are equipped with a form of suspension damping control. They may use hydraulic fluid, air, gas or be electrically controlled. The two most widely used internal designs are twin-tube and mono-tube.
Twin-tube vs. Mono-tube
The mono-tube design has a single cylinder:
The cylinder is divided into two sections: A fluid area and a gas chamber. The piston and shaft move in the fluid portion. It uses one fluid valve assembly in the piston. The diameter of the single working cylinder and piston valve is larger than in a twin tube even though the outside dimensions of each may the same. There is no need for an air or gas in the fluid area so the valve can operate more responsively and without any aeration or performance fade. The high pressure gas chamber is separated from the fluid area by a floating piston & seal. That provides an expansion area for the excess fluid movement during the compression stroke. On more aggressive movement the floating piston is pushed further into the gas chamber which increases gas pressure quickly and provides additional damping force. Because of its higher performance capabilities, the mono-tube design is used as original equipment on some vehicles and offered as an upgrade on vehicles that came equipped with the twin tube design.
The twin-tube design has two cylinders:
The inner, or working cylinder, is where the piston and shaft move up and down. The outer cylinder serves as a reservoir for the hydraulic fluid. There are fluid valves in the piston and in the stationary base valve. The base valve controls fluid flow between both cylinders and provides some of the damping force. The valves in the piston control most of the damping. The term Gas Shock usually refers to the same twin-tube design, but with one improvement. Low pressure Nitrogen gas is added to replace any oxygen air. The effect lessens aeration and performance fade.
All vehicles are equipped with a form of suspension damping control. They may use hydraulic fluid, air, gas or be electrically controlled. The two most widely used internal designs are twin-tube and mono-tube.
Twin-tube vs. Mono-tube
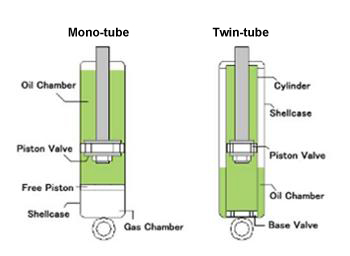
The cylinder is divided into two sections: A fluid area and a gas chamber. The piston and shaft move in the fluid portion. It uses one fluid valve assembly in the piston. The diameter of the single working cylinder and piston valve is larger than in a twin tube even though the outside dimensions of each may the same. There is no need for an air or gas in the fluid area so the valve can operate more responsively and without any aeration or performance fade. The high pressure gas chamber is separated from the fluid area by a floating piston & seal. That provides an expansion area for the excess fluid movement during the compression stroke. On more aggressive movement the floating piston is pushed further into the gas chamber which increases gas pressure quickly and provides additional damping force. Because of its higher performance capabilities, the mono-tube design is used as original equipment on some vehicles and offered as an upgrade on vehicles that came equipped with the twin tube design.
The twin-tube design has two cylinders:
The inner, or working cylinder, is where the piston and shaft move up and down. The outer cylinder serves as a reservoir for the hydraulic fluid. There are fluid valves in the piston and in the stationary base valve. The base valve controls fluid flow between both cylinders and provides some of the damping force. The valves in the piston control most of the damping. The term Gas Shock usually refers to the same twin-tube design, but with one improvement. Low pressure Nitrogen gas is added to replace any oxygen air. The effect lessens aeration and performance fade.
Loading...

Loading...
Loading...

Loading...

Loading...

Loading...

Loading...